リテール領域で
新たな拡販戦略を実行
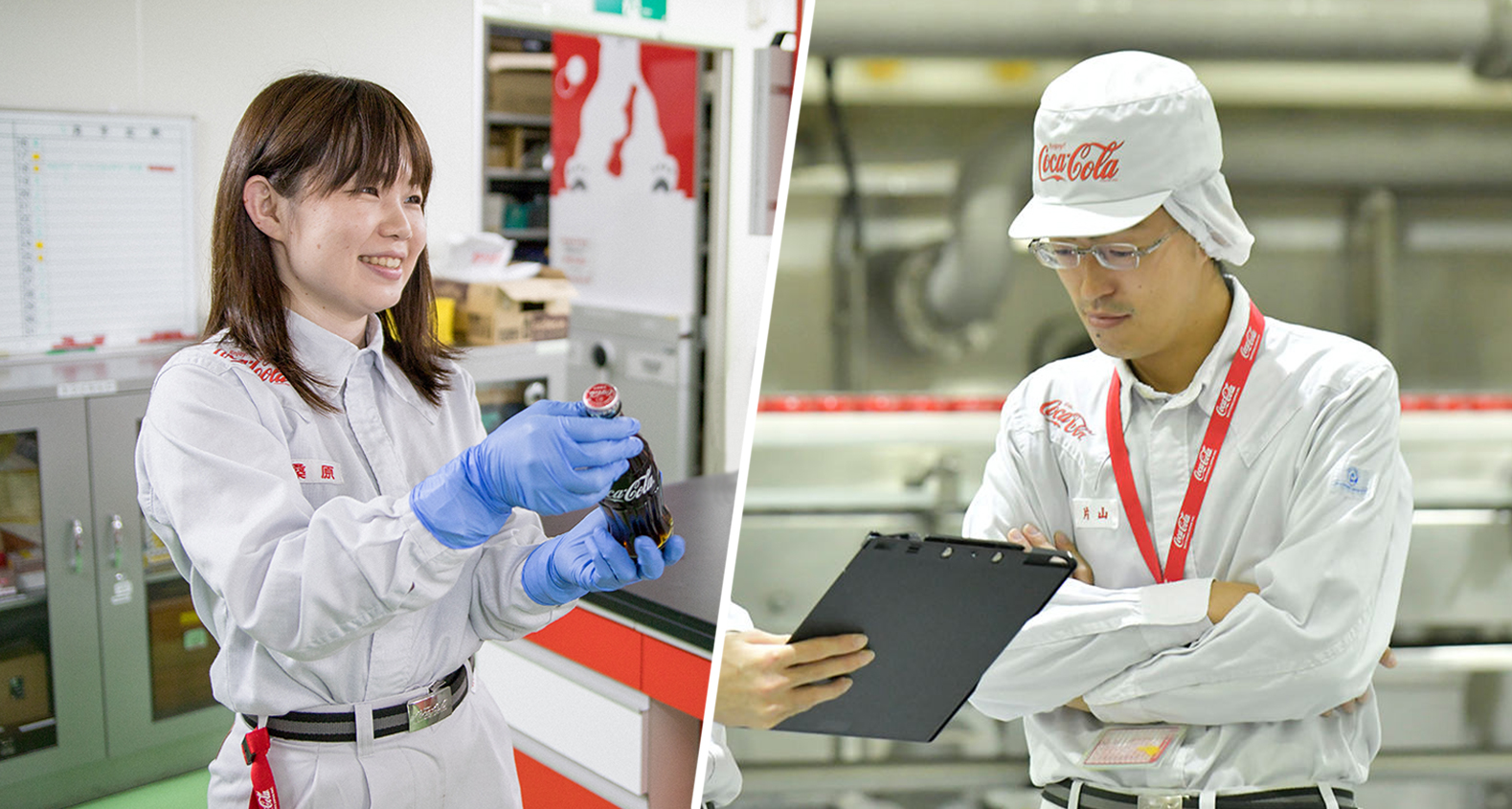
PROJECT STORY理系特集
改善プロジェクト
「今まで」を当たり前と思わずに、
「より良い仕組み」に挑む
製造・物流を担当するSCM本部では年に1回、各工場、部署において改善活動を行った成果を発表・共有する発表会を実施しています。2017年、埼玉工場で行われたひとつのプロジェクトが最優秀賞を受賞。効果金額自体は決して高額ではないその取り組みが評価を得たのは、他の工場で応用できる汎用性の高さでした。
01
品質管理の聖域
洗浄工程に改善の余地はあるのか?
多様な製品ラインナップを持ち、かつ、賞味期限1年以内のものが多い清涼飲料を製造しているコカ・コーラ ボトラーズジャパンには少ロット多品種製造を行う工場が多くあります。小ロット多品種製造の場合、製造品種の切り替え頻度が増えるため、洗浄や金型を変える作業が必要となり、業務負担やコストが増えてしまうことが全社的な課題として取り上げられていました。
そうした中、品質管理課マネージャーを中心に、この製品切り替え作業時に発生するコスト削減を目指すプロジェクトが立ち上がり、品質管理課のメンバーをプロジェクトリーダーとして、今回の取り組みがスタートしました。
製品切り替えの際の「洗浄工程」は非常に重要な工程であり、その手順は厳密に定められています。そのため、今回のテーマを聞いた2人が最初に思ったのは「そんなことができるのだろうか」ということでした。しかし、具体的な手法を考えるうちに、「洗浄工程は、絶対的な聖域だと思い込んでいただけかもしれない。今の手順よりも、もっと良い手順を自分たちで考え、実証し、実現させるチャンスじゃないか」と思い至りました。
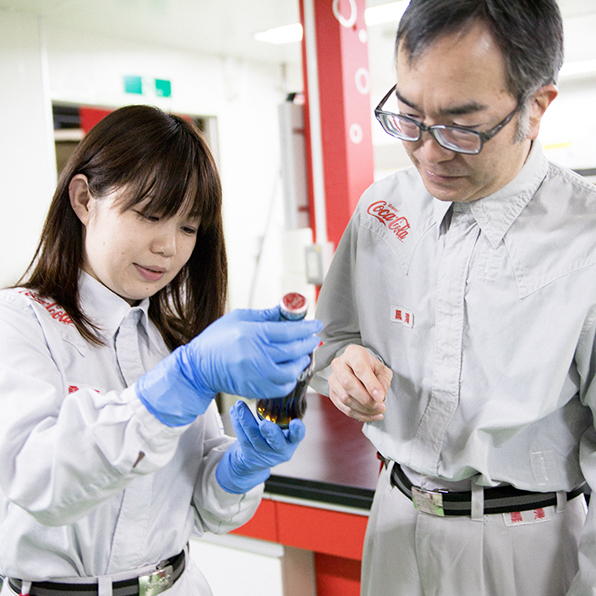
02
立ちはだかる製造と検証両立の難しさ
工場のメンバーが一丸となって協力
上司や社内のメンバーに相談しながら新しい手順のパターンをいくつか検討した後、実際に検証をする段階になって2人を悩ませたのは、どの製品の製造後に新しい洗浄手順の検証を行うかということでした。
例えば、コーヒー製品だけでも砂糖、ミルクの有無やフレーバーの違いなど10種類以上にもなります。プロジェクトリーダーは上司からのアドバイスを参考に、製造後、最も製品液が残りやすく、香りの強い製品を選び、その製品の製造後に新しい洗浄手順を試して問題がなければ、他の製品にも対応できるだろうと考え、具体的な検証計画を立て始めました。新しい手順の安全性や確実性を実証するのに必要な検証回数や洗浄前の生産量などを検討していくのですが、洗浄工程の検証は、該当製品を製造した後にしか実施できません。そのため工場内の生産計画担当者や、製造ラインの担当者などあらゆる関係者からの協力を仰ぎ、通常の製造活動の妨げにならないよう調整しながら検証を行う必要がありました。
実際に検証を始めたのが2月で、成果が見え始めたのが4月、当時は焦る気持ちを抱えながら様々な洗浄手法を試し、データを分析し続けたといいます。「出荷する製品を製造している設備で実験を行う以上、当然ながら、新しい手法での洗浄に加えて、既存の洗浄も実施しなければならず、検証中は2倍の作業量と時間を使う事になりました。工場のメンバーには本当にたくさんの協力をしてもらいました」とプロジェクトリーダーは振り返ります。
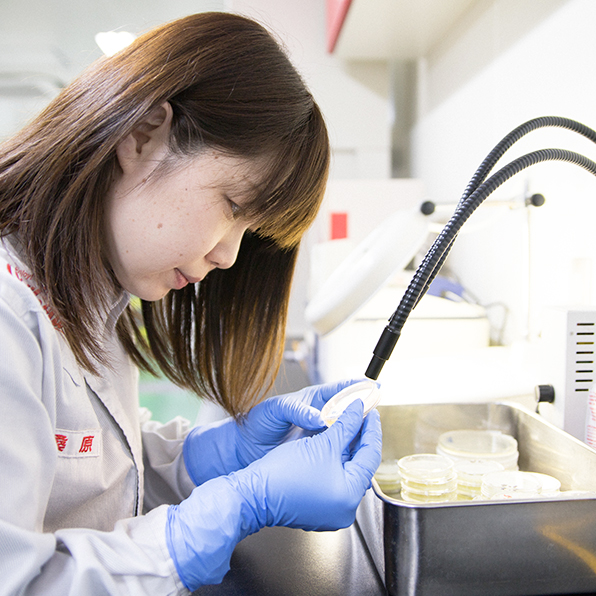
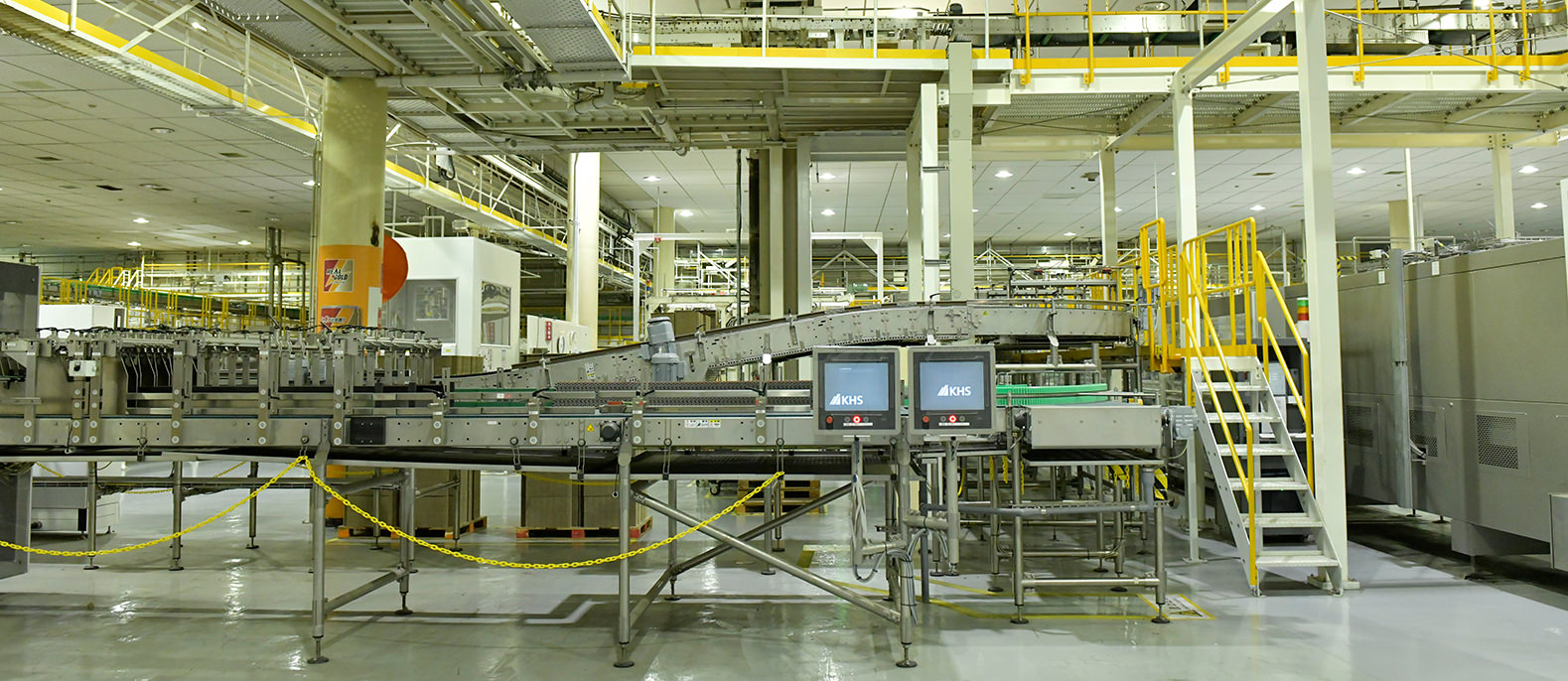
03
課題を丁寧に取り除きながら進んだ検証
汎用性の高さで最優秀賞を受賞
新しい手順を検討しては検証を繰り返す中で、最後の障壁となったのは、検証結果のばらつきでした。同じ担当者、同じ条件で洗浄しているのにもかかわらず検証結果に差が出てしまったのです。そこで、改めて作業工程を一つずつ細かくチェックしていくと、ある作業で使用していた検査キットの活用方法に課題がある事がわかりました。その部分を改善して検証したところ、検証結果も安定し、確実なデータを収集することに成功。ようやく新しい手順を確立するに至ったのでした。
手順が定まると、プロジェクトメンバーは今回の成果を他の工場に情報共有するため、改善活動の発表会に参加する事を決意。さっそく準備に取り掛かりました。この発表会には製造部以外の社員もゲストとして招かれるため、誰にでもわかるように取り組み内容や成果を説明しなければなりません。また、たくさんのプロジェクトが紹介される中で聴衆の印象に残るためには、興味をもってもらえるようなプレゼンテーションが求められます。「資料だけでなく、各チームが色々な準備をして発表に臨むので、ある意味、検証作業より大変だったかもしれません笑」とプロジェクトメンバー。ユーモアを交えた説明を加えるなど工夫した結果、洗浄工程の改善プロジェクトは、東日本地区の大会で1位をとり、全国大会でも最優秀賞を獲得しました。
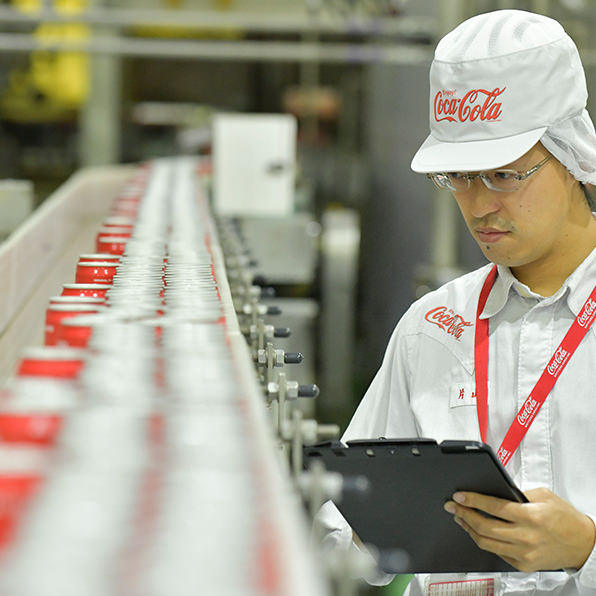
04
ひとつの取り組みが多くの工場に広がり
大きな結果を生み出す
今回のプロジェクトについて「珍しい取り組みではあるけど優勝するほどではないだろう」と思っていたプロジェクトメンバー。少量生産に対する取り組みだったため、手順を変えたことで削減できたコストの金額が低かったのです。「他の発表では億単位の改善プロジェクトもあったので敵わないだろうと思っていました。」 しかし、少量生産による課題はどの工場も共通の悩み。各工場が同じように手順を変えれば多くの工場に応用が可能という、その圧倒的な汎用性が評価されました。
改善プロジェクトを終えた今、プロジェクトリーダーは「製造や品質管理の工程には決まりごとが多いのですが、それを当たり前と思わず、失敗してもいいからチャレンジし続ける姿勢が大事なのだと気付きました」と話します。また、上司であるマネージャーは「地道な改善活動にスポットを当てた発表会や表彰は、私たち社員のモチベーションのアップにつながります。現場の改善を上司や周りに提案できる事は、当社でエンジニアとして働く醍醐味だと思うので、今後も積極的に取り組んでいきたい」と次の挑戦に期待をこめました。
改善プロジェクトは、コカ・コーラ ボトラーズジャパンの文化です。現場社員のひとつひとつの取り組みが全工場へと広がっていきます。
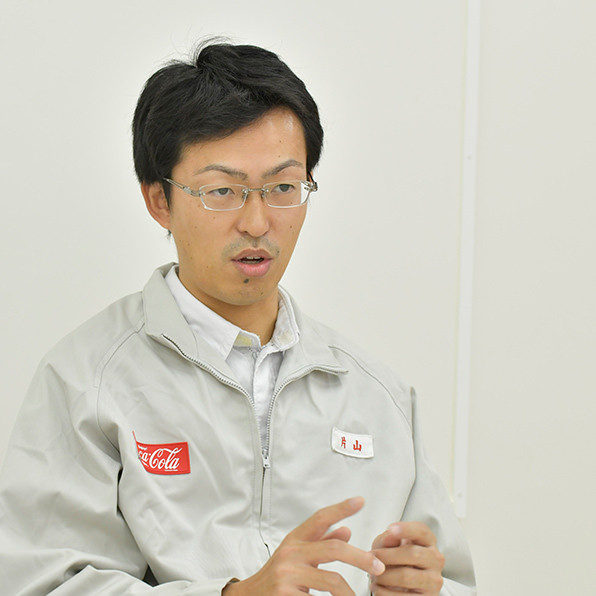
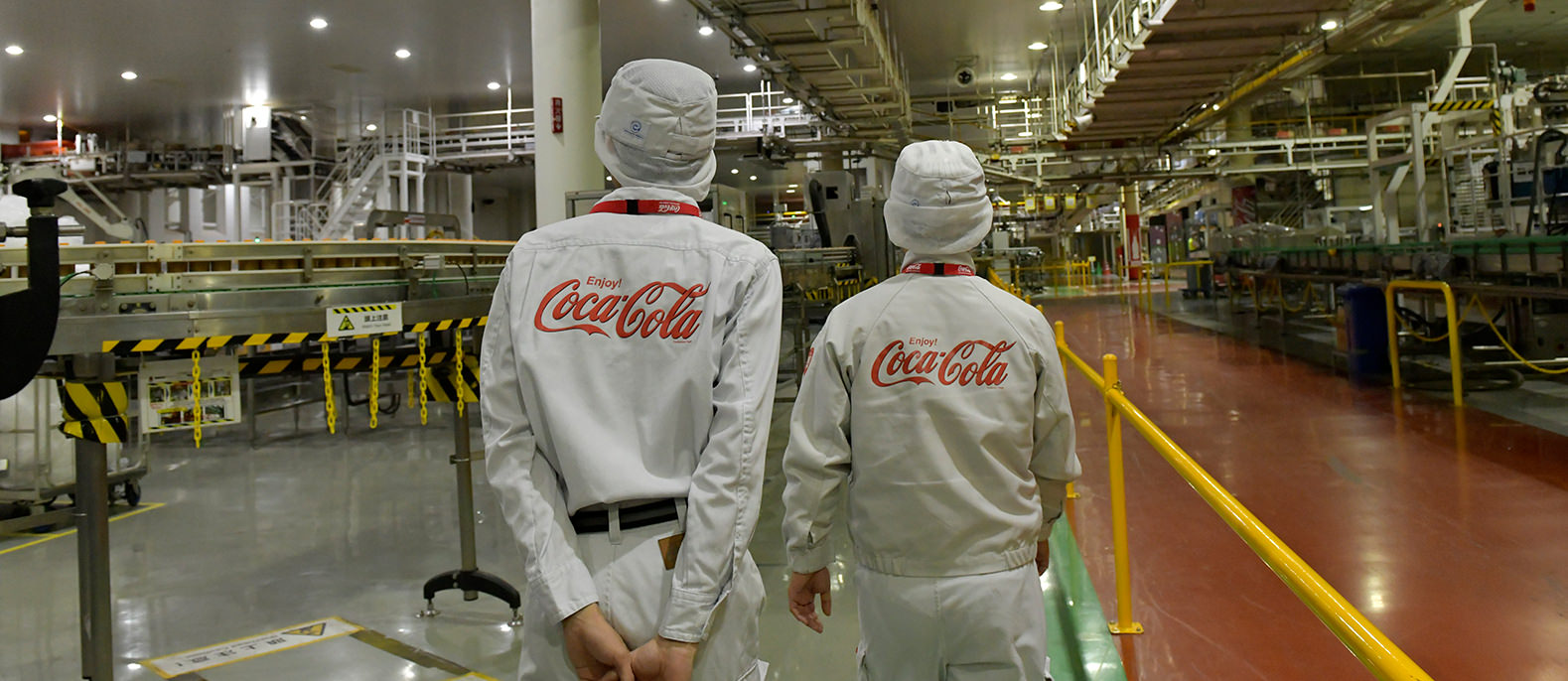
PROJECT MEMBER
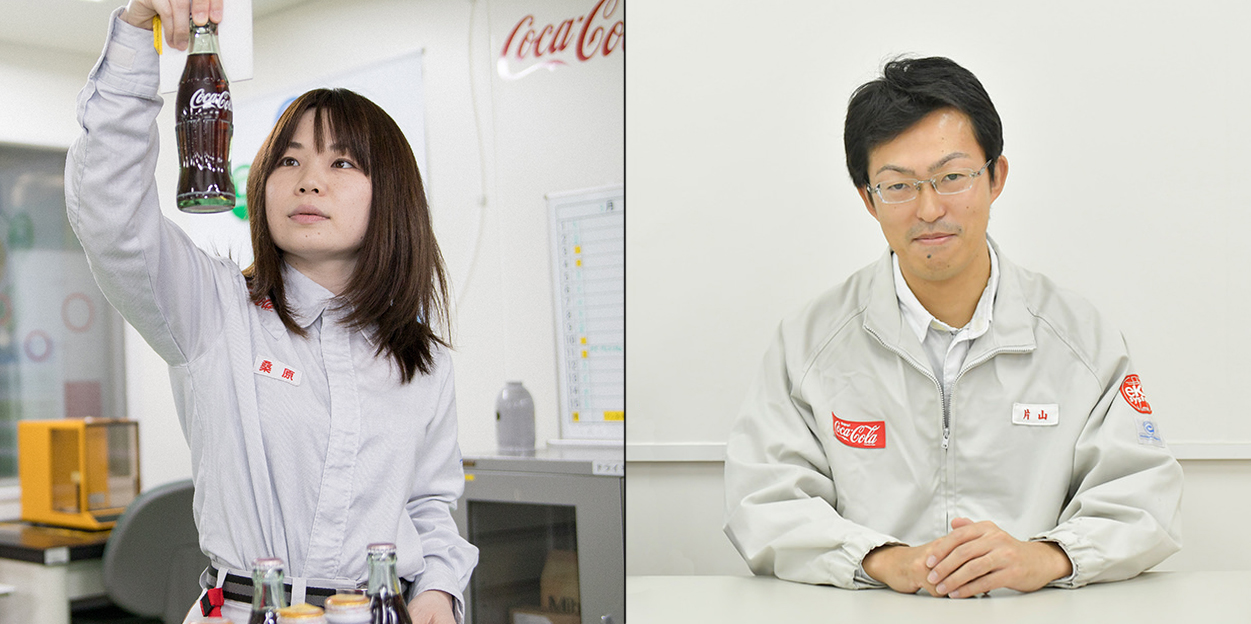
(左)Satoe.K
SCM本部 製造統括部 品質管理担当
2007年入社
(右)Junji.K
埼玉工場 品質管理課 マネージャー
2008年入社/理工学部卒